Hakkımızda
Gıda güvenliği ve kalite kontrolü, sağlıklı bir yaşam için büyük önem taşımaktadır. Gıda analiz laboratuvarımız, gelişmiş teknolojiler ve uzman kadrosuyla, gıda ürünlerinin güvenilirliğini sağlamak ve kalite standartlarını korumak amacıyla hizmet vermektedir. Bilimsel doğruluk ve titizlikle gerçekleştirdiğimiz analizler sayesinde, tüketicilere güvenli gıda sunulmasına katkıda bulunuyoruz.
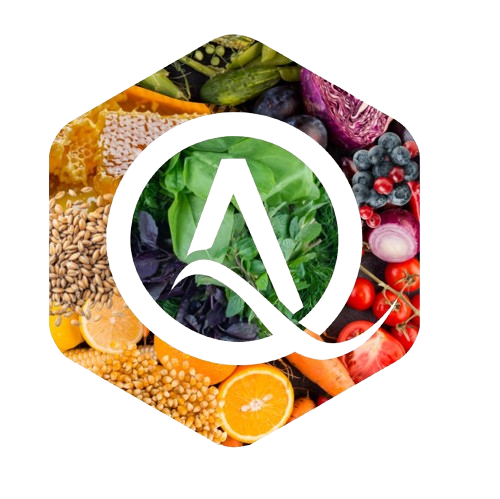